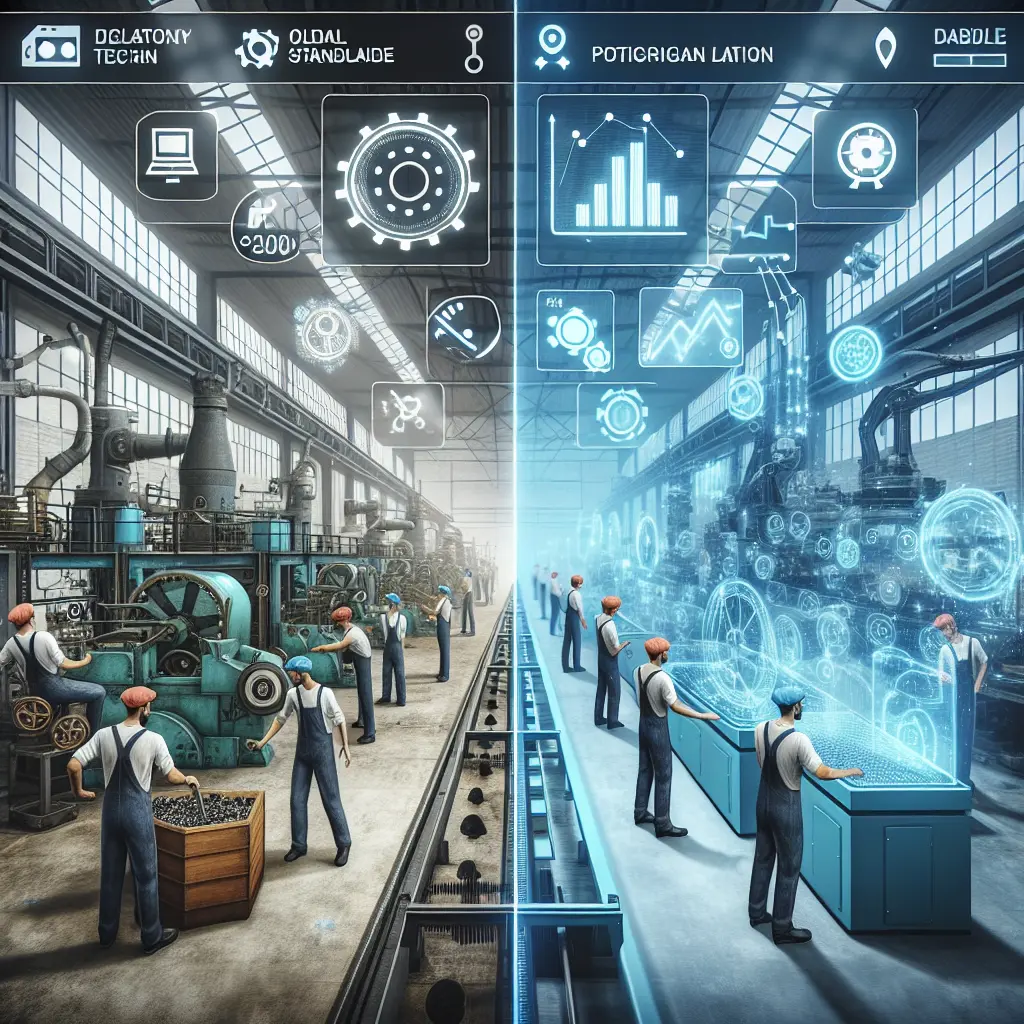
The world of manufacturing is undergoing a seismic shift, thanks to advancements in technology. At the heart of this revolution is the emergence of Digital Twins, a technology that is fundamentally transforming how industries approach maintenance, efficiency, and innovation. In this post, we'll delve into how Digital Twins are revolutionizing predictive maintenance in manufacturing industries, driving unprecedented levels of operational efficiency and cost reduction.
The Rise of Digital Twins in Industry 4.0
Digital Twins have become a cornerstone of Industry 4.0, mirroring physical assets, systems, or processes to create a real-time digital counterpart. This technology not only provides a visual representation of machinery but also enables real-time data analysis, predictive analytics, and maintenance optimization. As the manufacturing sector increasingly adopts IoT in manufacturing, the integration of Digital Twins with these technologies enhances asset management and operational efficiency dramatically.
Integrating Predictive Maintenance with Digital Twin Technology
Predictive Maintenance stands out as one of the most impactful applications of Digital Twins in manufacturing. By leveraging IoT sensors and machine learning algorithms, Digital Twins can predict when equipment will fail or need maintenance. This foresight allows for maintenance optimization, ensuring that machinery is serviced only when necessary, thus reducing downtime and extending the lifespan of equipment.
Case Study: Smart Manufacturing and Maintenance Optimization
Consider the application of Digital Twins in automotive manufacturing, such as the assembly lines that produce vehicles like the 2025 Lincoln Navigator. This model is not just a luxury vehicle but a testament to advanced manufacturing technologies. Equipped with a "rolling spa" feature and a massive digital dash, the Navigator showcases how luxury and technology can merge to enhance user experience. The vehicle's production process, supported by Digital Twins, exemplifies how real-time data analysis and predictive maintenance can streamline production and increase manufacturing efficiency.
Digital Twin Implementation: A Look at Recent Advancements
Recent news highlights significant strides in digital transformation in manufacturing. The People's Bank of China's efforts to promote high-quality financial development indirectly supports technological investments in manufacturing sectors, facilitating smoother implementation of advanced technologies like Digital Twins.
Furthermore, companies like Globant and Super League Enterprise have shown through their earnings calls that technology-driven strategies are central to maintaining competitive edges in today’s markets. These discussions underline the importance of integrating Digital Twins with existing corporate strategies to enhance operational efficiency.
Leveraging Predictive Analytics and Machine Learning
The synergy between machine learning in manufacturing and Digital Twins creates a potent tool for predictive analytics. By analyzing patterns from historical data, machine learning algorithms can forecast potential failures before they occur, thereby informing predictive maintenance schedules. This capability not only prevents costly downtime but also optimizes the use of resources.
Digital Twin Technology and IoT in Manufacturing
IoT devices play a crucial role in feeding real-time operational data to Digital Twins. This data is critical for the accurate simulation and analysis that Digital Twins provide. In smart manufacturing ecosystems, this integration facilitates not only maintenance but also operational decisions that enhance efficiency and reduce costs.
Cost Reduction Strategies through Efficient Asset Management
Effective asset management is crucial for reducing costs in manufacturing. Digital Twins offer a detailed overview of asset health and operational performance, allowing for better capital planning and resource allocation. This strategic approach leads to significant cost savings by avoiding unnecessary expenditures and focusing on essential maintenance and upgrades.
Operational Efficiency Through Advanced Manufacturing Technologies
The broader scope of operational efficiency achievable through Digital Twin technology is vast. It extends beyond predictive maintenance to encompass the entire manufacturing process. By simulating different production scenarios, manufacturers can identify the most efficient processes, thereby reducing waste and increasing productivity.
Maintenance Technology Trends: What’s Next?
As we look to the future, the evolution of maintenance technology seems intertwined with advancements in Digital Twins. The integration of augmented reality (AR) and virtual reality (VR) with Digital Twin technology promises even more immersive and intuitive interfaces for managing and maintaining equipment. These developments could redefine training processes and operational protocols within manufacturing industries.
Conclusion: The Transformative Impact of Digital Twins on Manufacturing
The integration of Digital Twins into manufacturing signifies more than just an upgrade in technology—it marks a paradigm shift in how industries operate. Predictive maintenance powered by Digital Twins not only enhances asset life and reduces costs but also propels the entire sector towards unprecedented levels of precision and efficiency.
As we continue to witness innovations like those seen in the 2025 Lincoln Navigator or the strategic initiatives by global financial systems like China's PBOC, it is clear that the path forward for manufacturing is heavily digitized and optimized. The journey towards smarter manufacturing practices is well underway, promising a future where downtime and inefficiency become relics of the past.
By embracing these advanced manufacturing technologies, industries can not only predict future challenges but also prepare to meet them head-on. As we forge ahead, let’s continue to innovate and integrate these transformative technologies into our daily operations.
— Helen Baxter
For further reading on Smart Manufacturing More on Predictive Maintenance Techniques